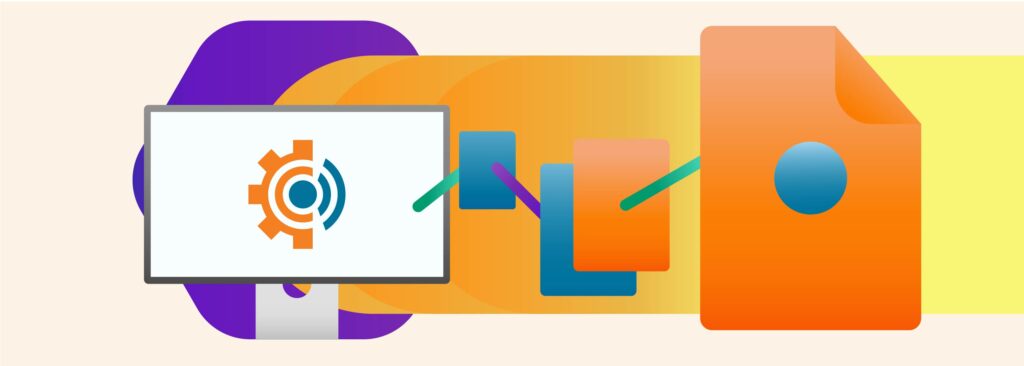
The outlook for facility managers, maintenance managers, and property management professionals is improving. Currently, organizations in the facilities management industry generate around $1.2 trillion, and this figure should grow at a compound annual growth rate exceeding 4%. Consequently, this growth highlights the increasing importance of digital tools in streamlining business operations. Therefore, management teams need a powerful tool to simplify complex processes.
To achieve this, the goal is to implement a software system that provides real-time data collection and critical notifications. For example, with a user-friendly mobile app, users can complete tasks such as scheduling service requests, checking inventories, and accessing historical data with ease. Additionally, field technicians equipped with mobile phones can efficiently communicate with maintenance teams across multiple facilities. As a result, this reduces the need for phone calls and enables immediate data collection.
Furthermore, computerized maintenance management systems (CMMS) are essential for integrating maintenance operations. In particular, mobile work order software is critical for maintenance contractors and small business maintenance companies.
Industry-Specific Software for Business
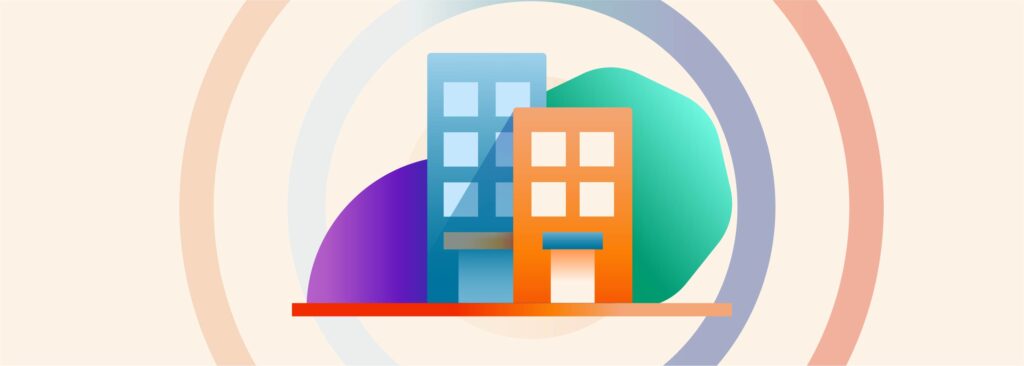
Both large and small businesses recognize the benefits of software systems. Notably, these systems save money, track progress, and provide instant access to accurate information. Specifically, they expedite maintenance requests, reduce travel time, and simplify work request tracking. Moreover, customers value web-based applications that allow them to log in and access a central location for service requests.
Consequently, software developers are increasingly creating solutions that integrate customer, employee, data, and asset management. In addition, industry-specific software is now prevalent in major vertical markets, catering to specialized niches such as credit unions, online technical schools, and maintenance departments in various industries. Therefore, a well-designed software solution gives organizations a competitive edge by addressing unique needs.
What is a Work Order
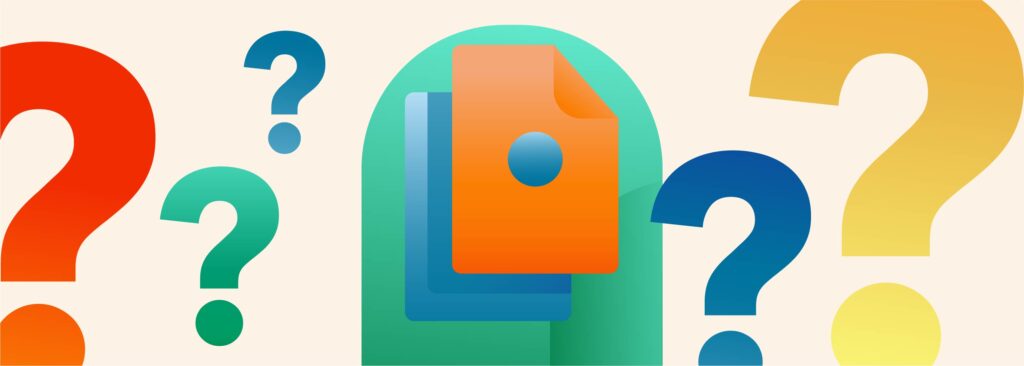
Work orders are crucial for service-based businesses. Essentially, they represent formal requests for services, such as addressing leaks or equipment malfunctions. Traditionally, businesses communicated work orders through written documents; however, modern systems now use technology for efficient management.
The Basic Work Order Process
In most organizations, the work order process involves a series or set of logical phases such as follows:
Defining the task: The initial step involves defining the service need, i.e., spill, leak, or malfunction.
Order creation: Here, the worker order information is properly specified with details including location, timing, etc.
Formal approval: In many organizations, a maintenance manager, operations supervisor, or another individual provides written confirmation of approval.
Transmittal of the order: The work order is forwarded to the appropriate recipient, which might specify an emergency designation.
Performance of the order: The service professional assesses the issue and performs the needed work.
Review and closure: The work order is transitioned to some final status of completion and might be reviewed by appropriate parties.
Key Elements of a Work Order
A work order should include the date, location, and a detailed summary of the task. Often, it involves documenting the maintenance or repair assessment and any necessary supplies. Furthermore, each work order receives a unique job or ID number, which is crucial for tracking and referencing.
Types of Work Orders
Several types of work orders exist; however, they serve the same purpose of communicating information for business purposes. Having a set or formalized process allows for uniformity and tends to reduce errors. Work orders are often categorized according to the nature of the work request.
Reactive Work Orders: These address unexpected issues and may be emergency-related. For instance, condition-based maintenance (CbM) and predictive maintenance fall into this category.
Preventative Maintenance Work Orders: These serve as reminders to perform routine checks or service tasks according to a scheduled plan.
Predictive Maintenance Work Orders: These use sensors to monitor asset conditions and predict maintenance needs.
Types of Work Order Management Software Systems
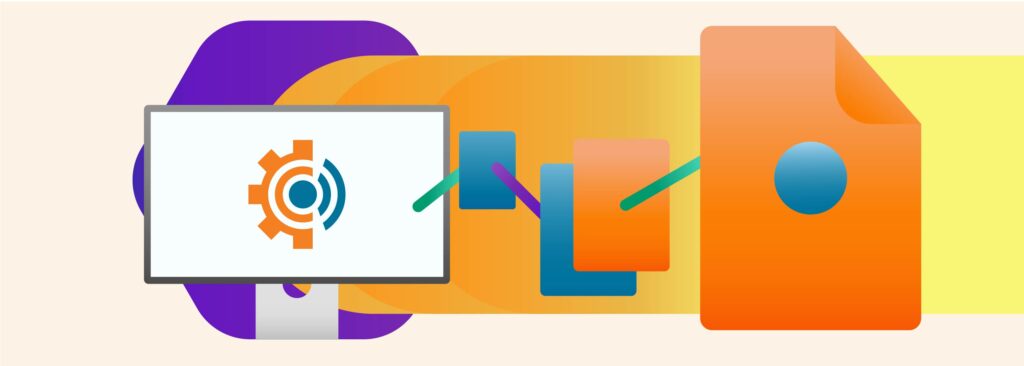
Simple Work Order Software Systems: These are suitable for small businesses, offering basic maintenance management functionalities.
Computerized Maintenance Management Systems (CMMS): Typically designed for larger businesses, these systems offer comprehensive features, including preventative maintenance and data management.
Field Management Systems (FSM): These support field technicians with real-time access to information and resources, thus enhancing off-site task management.
Enterprise Asset Management (EAM) Software: This tracks assets from purchase to disposal, focusing on maximizing service life and minimizing downtime.
Powerful, Cloud-Based Software for Automating Commercial Facility Maintenance Activity
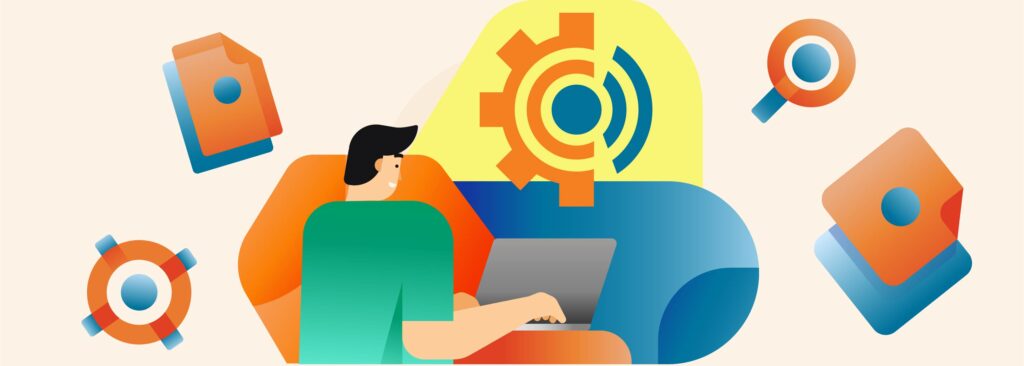
Ranyan offers a dynamic software solution for janitorial, property maintenance, and engineering services. Implementing Ranyan transforms operations into a streamlined, automated model. Thanks to its cloud-based system, it manages work orders, employee schedules, and multiple job sites in real-time. As a result, it transitions to paperless workflows and provides an easy-to-use digital client portal.
Get in Touch with Us for Seamless Facility Management Solutions
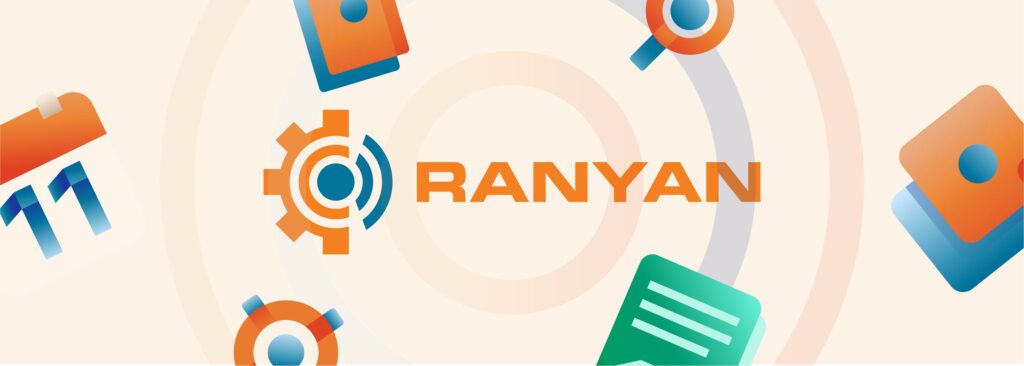
As the outlook improves for facility managers, maintenance managers, and property management professionals, Ranyan stands out as a vital tool for simplifying complex processes. Our advanced software system offers real-time data collection and notifications, enhancing efficiency and workflow. Whether you’re handling maintenance tasks, scheduling service requests, or checking inventories, our solution integrates seamlessly with your operations.
To explore how Ranyan can transform your facility management experience, we invite you to reach out. For inquiries, support, or to schedule a demo, contact us today.
Phone: +1 786-297-8830
Email: info@ranyan.com
We look forward to helping you streamline your facility management and improve your operational efficiency.